Fast and Affordable Packaging Machine Repair Services You Can Rely On
Quick and Reliable Packaging Device Repair Service Solutions to Decrease Downtime
In the competitive landscape of manufacturing, the effectiveness of packaging procedures pivots on the integrity of machinery. Quick and trustworthy repair services are vital in minimizing downtime, which can lead to considerable operational problems and monetary losses.
Relevance of Timely Repairs
Timely repair services of packaging devices are important for preserving operational effectiveness and decreasing downtime. In the fast-paced setting of production and product packaging, also minor breakdowns can result in substantial delays and efficiency losses. Dealing with concerns promptly ensures that devices run at their ideal capability, therefore protecting the circulation of operations.
In addition, normal and timely maintenance can protect against the rise of minor issues into significant breakdowns, which frequently sustain higher repair prices and longer downtimes. A positive technique to maker repair not only preserves the integrity of the tools but likewise improves the overall dependability of the assembly line.
Additionally, prompt repairs add to the long life of packaging machinery. Machines that are serviced without delay are much less likely to deal with excessive wear and tear, enabling companies to maximize their investments. This is specifically essential in sectors where high-speed packaging is crucial, as the demand for constant performance is extremely important.
Advantages of Reliable Company
Trustworthy provider play a crucial duty in making sure the smooth operation of product packaging makers. Their experience not only enhances the efficiency of fixings but additionally adds significantly to the longevity of tools. Reliable provider are furnished with the technical knowledge and experience necessary to detect problems properly and execute effective options quickly. This decreases the threat of repeating problems and makes sure that makers run at optimal efficiency levels.
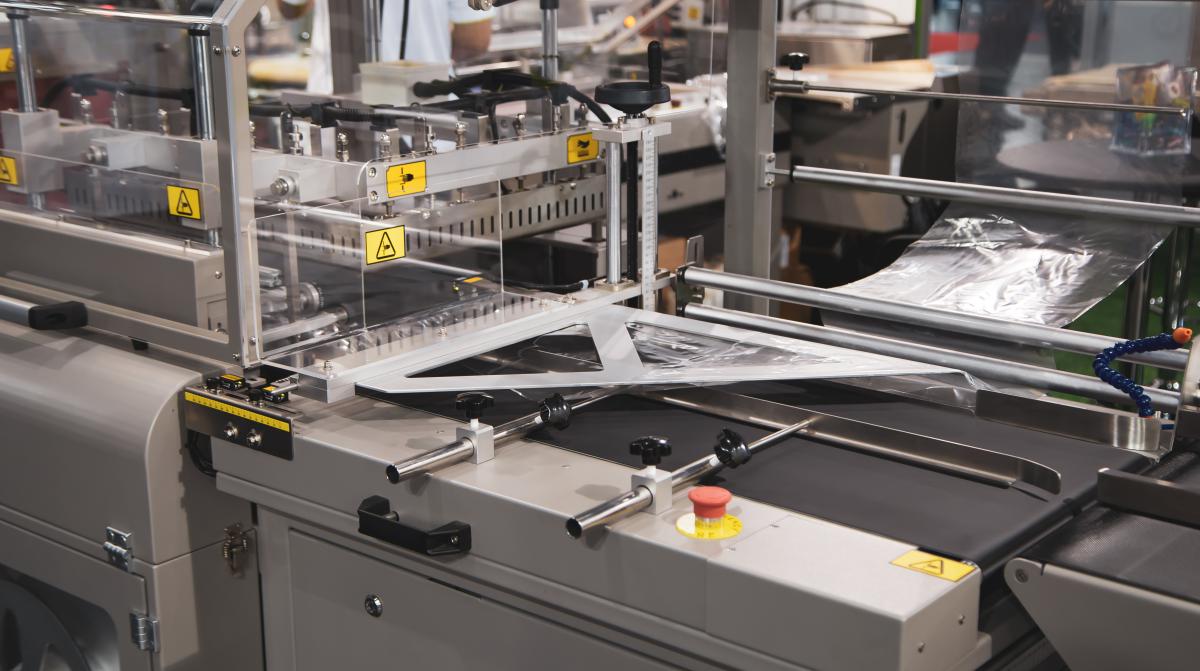
Additionally, a respectable provider uses detailed support, consisting of training and advice for staff on maker operation and maintenance best methods. This not just encourages staff members but additionally grows a society of safety and performance within the organization. In general, the advantages of involving dependable company expand beyond instant repair services, positively affecting the whole operational process of product packaging processes.
Usual Product Packaging Machine Issues
In the realm of packaging operations, numerous problems can compromise the effectiveness and functionality of devices. One widespread issue is mechanical failure, commonly originating from deterioration or inadequate maintenance. Components such as motors, belts, and equipments might fail, leading to failures that stop manufacturing. One more common issue is imbalance, which can trigger jams and unequal packaging, impacting product high quality and throughput.
Electrical problems can additionally interfere with product packaging procedures. Malfunctioning circuitry or malfunctioning sensing units might cause unpredictable machine habits, triggering delays and enhanced operational expenses. In addition, software problems can prevent the device's programming, resulting in functional ineffectiveness.
Irregular item flow is an additional vital problem. This can arise from variants click site in item shape, size, or weight, which might influence the equipment's capability to deal with products precisely. Insufficient training of drivers can worsen these troubles, as untrained personnel may not acknowledge early indicators of malfunction or might abuse the devices.
Resolving these typical packaging maker problems without delay is important to preserving efficiency and guaranteeing a smooth procedure. Routine assessments and aggressive upkeep can significantly alleviate these issues, fostering a dependable product packaging setting.
Tips for Decreasing Downtime
To lessen downtime in product packaging operations, carrying out an aggressive maintenance method is crucial. Frequently set up maintenance checks can identify prospective problems before they rise, ensuring equipments operate efficiently. Establishing a regimen that consists of lubrication, calibration, and assessment of important components can considerably reduce the find out this here frequency of unforeseen break downs.
Training staff to run equipment properly and recognize very early warning indications of malfunction can also play a vital duty. Equipping drivers with the knowledge to carry out standard troubleshooting can protect against minor issues from triggering significant hold-ups. Moreover, preserving a well-organized supply of essential spare components can expedite repairs, as waiting for parts can result in extensive downtime.
Furthermore, documenting equipment performance and maintenance activities can help determine patterns and persistent troubles, permitting for targeted interventions. Integrating sophisticated tracking innovations can give real-time information, allowing anticipating upkeep and minimizing the risk of abrupt failures.
Lastly, cultivating open interaction between drivers and maintenance groups guarantees that any abnormalities are promptly reported and dealt with. By taking these aggressive procedures, companies can improve operational efficiency and considerably reduce downtime in packaging procedures.
Choosing the Right Fixing Solution
Picking the proper repair service for product packaging equipments is an important choice that can dramatically influence functional effectiveness. Begin by evaluating the copyright's experience with your particular kind of product packaging devices.
Next, consider the provider's reputation. Seeking responses from other organizations within your sector can provide insights right into integrity and quality. Certifications and partnerships with identified devices manufacturers can also show a commitment to excellence.
Additionally, analyze their action time and accessibility. A provider who can provide timely assistance minimizes downtime and keeps production circulation consistent. It's also critical to ask about guarantee and service assurances, which can show the confidence the copyright has in their job.

Final Thought
Finally, the significance of reputable and quick packaging maker repair service solutions can not be overstated, as they play a crucial role in decreasing downtime and guaranteeing operational performance. By focusing on prompt repairs and picking trustworthy solution carriers, companies can efficiently preserve and deal with common concerns performance. Implementing aggressive maintenance techniques and spending in team training more boosts the durability of packaging machinery. Ultimately, a strategic strategy to fix services cultivates a more resilient production environment.
Timely repair work of product packaging devices are vital for maintaining operational have a peek at this website performance and lessening downtime.Furthermore, timely fixings contribute to the durability of packaging equipment. Generally, the benefits of engaging trusted solution carriers expand beyond prompt fixings, positively impacting the entire operational workflow of packaging processes.
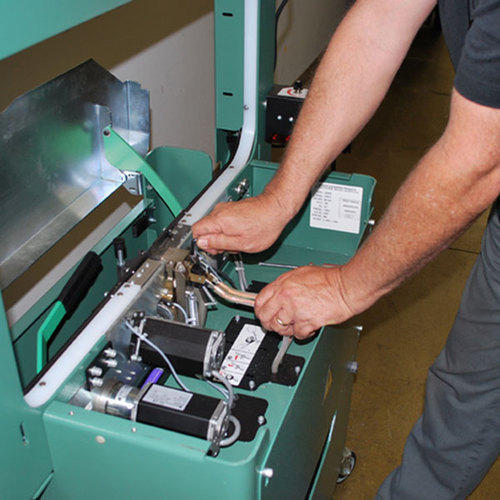